In the rapidly evolving landscape of manufacturing, factory digitization has become imperative for organizations striving to maintain a competitive edge. As technology continues to advance, mobile apps are emerging as powerful tools that streamline operations, enhance productivity, improve communication, and drive efficiency in manufacturing processes. Manufacturers are increasingly recognizing the importance of mobile technologies, with a survey conducted by PwC revealing that 70% of manufacturers believe mobile technologies are critical for future success and competitiveness. In this article, we will explore the pivotal role of mobile apps in factory digitization, shed light on the pain points associated with non-digitized manufacturing processes, and demonstrate how mobile apps, such as a ReadyKey App, can effectively address these challenges.
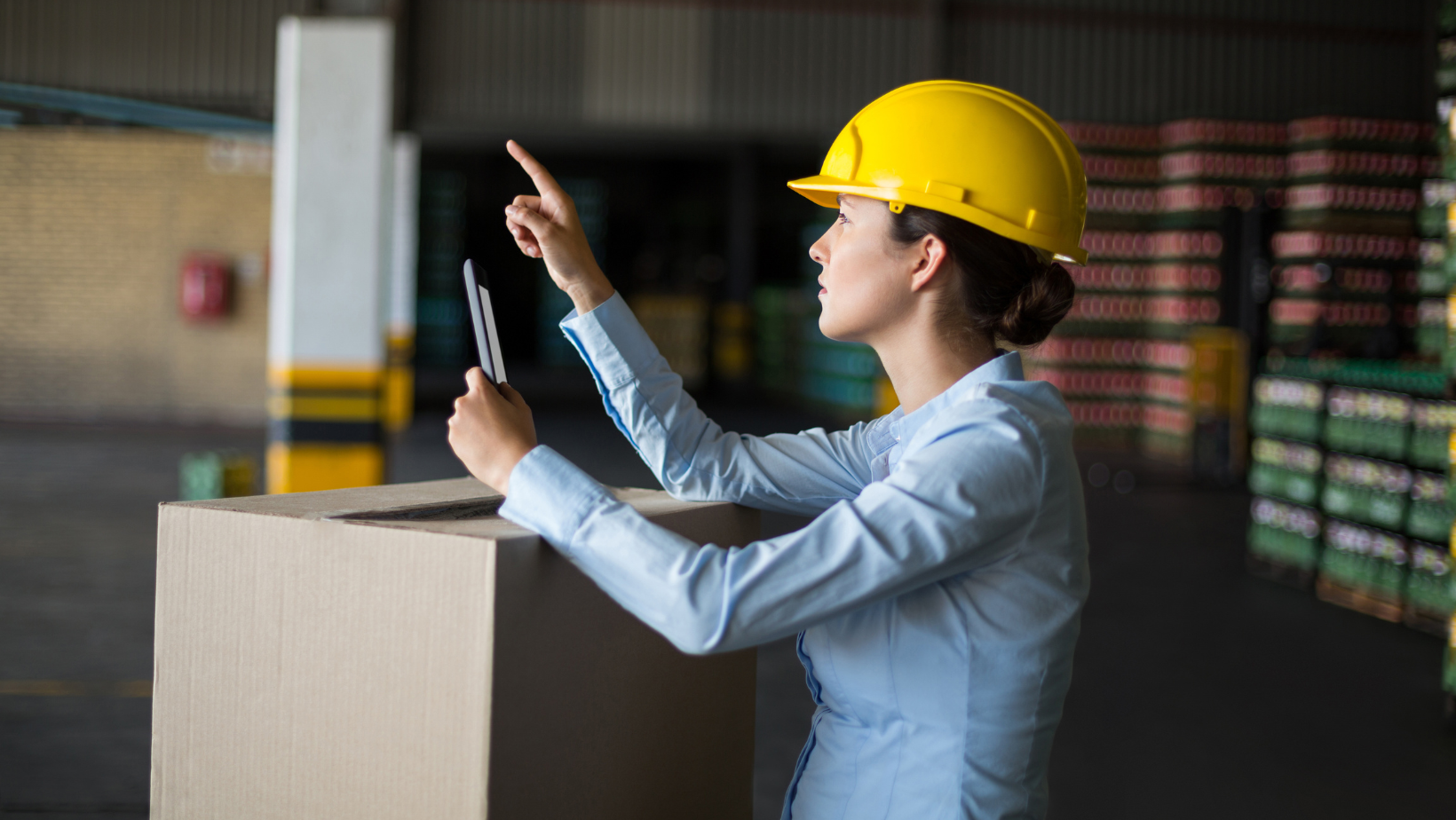
The Challenges of Non-Digitized Manufacturing Processes
Before delving into the benefits of factory digitization, it is crucial to understand the pain points and challenges faced by manufacturers who have not yet embraced digital transformation. Non-digitized manufacturing processes suffer from the following challenges:
Manual and Paper-Based Systems
Traditional manufacturing processes heavily rely on manual documentation and paper-based systems. This approach introduces inefficiencies, delays, and errors. Manual data entry and paper-based forms are time-consuming, prone to mistakes, and difficult to manage. Additionally, searching for specific information or retrieving historical data becomes a tedious and time-consuming task, hampering operational efficiency.
Lack of Real-Time Visibility
Non-digitized factories often struggle with real-time visibility into their operations. Without access to timely and accurate data, decision-making becomes challenging. Managers and employees are left in the dark, relying on outdated reports or verbal communication for critical information. This lack of real-time visibility effects the ability to respond quickly to issues, make informed decisions, and optimize production processes.
Communication Bottlenecks
In non-digitized manufacturing environments, communication bottlenecks are common. Important information often gets lost in translation or takes a significant amount of time to reach the intended recipients. Communication gaps between different teams, shifts, or factory locations can lead to delays, misunderstandings, and inefficiencies. These bottlenecks can negatively impact productivity, coordination, and overall operational performance.
Inefficient Data Collection and Analysis
Gathering and analyzing data is vital for driving continuous improvement in manufacturing. However, non-digitized processes relying on manual data collection methods, can often lead to inconsistent and incomplete data. Analyzing data becomes a cumbersome task, making it difficult to identify trends, spot anomalies, or make data-driven decisions. Without accurate and comprehensive data, manufacturers miss out on opportunities for optimization and cost reduction.
Limited Scalability and Adaptability
Non-digitized manufacturing processes often struggle with scalability and adaptability to changing market dynamics. Manual processes and paper-based systems impose limitations on expanding operations, integrating new technologies, or accommodating evolving customer demands. Manufacturers find it challenging to keep up with the pace of innovation and may face increased operational costs or decreased competitiveness.
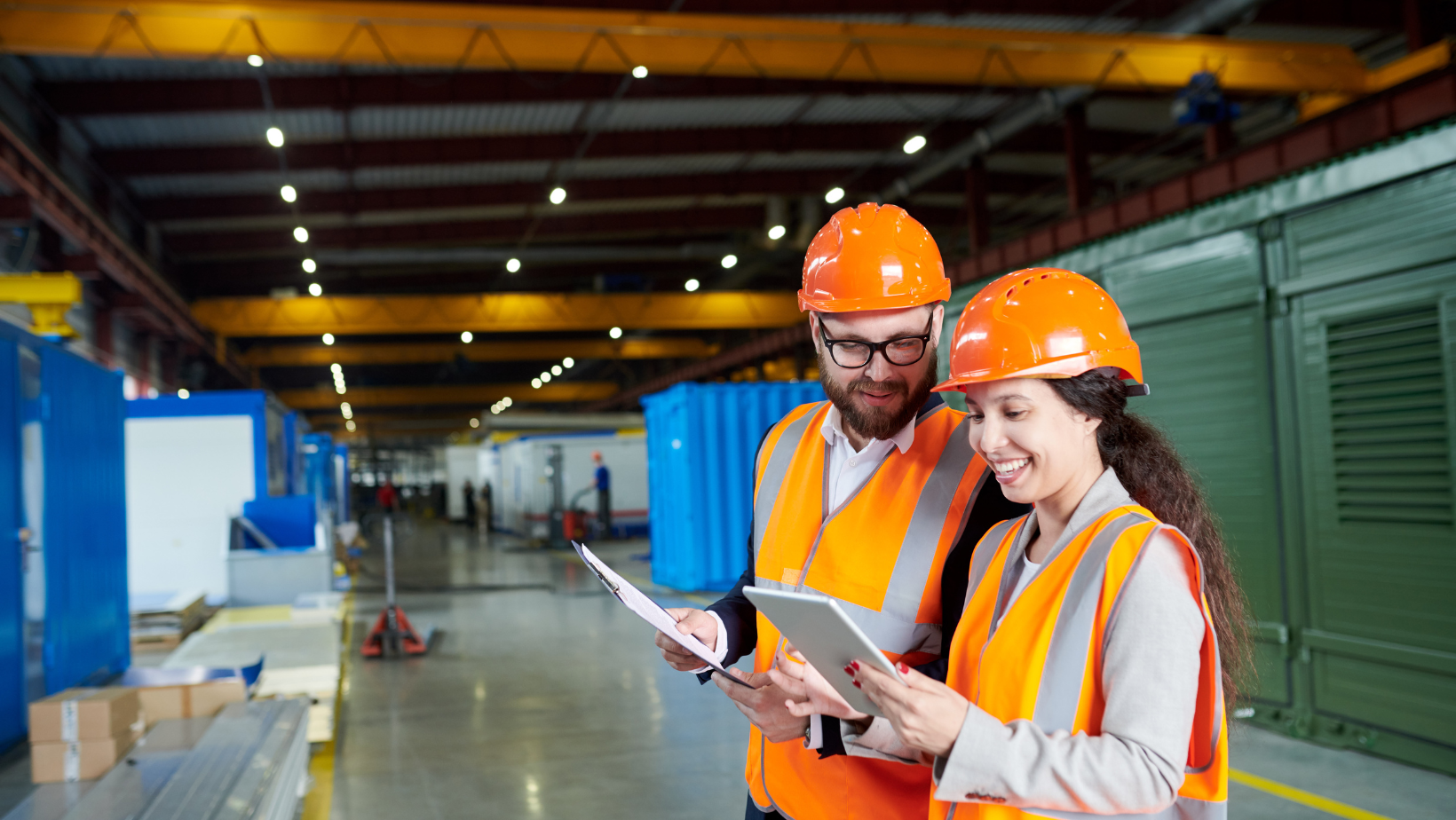
Empowering Productivity and Profits with Factory Digitization
Mobile apps, such as a Ready App, offer a powerful solution to overcome the challenges associated with non-digitized manufacturing processes. Here's how factory digitization can address these pain points:
Achieving Greater Efficiency
Factory digitization enables manufacturers to streamline operations, reduce manual errors, and optimize resource allocation. By providing real-time access to critical information, mobile apps empower employees to make data-driven decisions on the go. This increased efficiency translates into improved productivity, reduced downtime, and a competitive edge in the market. According to a study by McKinsey, digitized factories can experience a 20% increase in operational efficiency, highlighting the significant impact that mobile apps can have on productivity.
Enhancing Communication
Mobile apps break down communication barriers by facilitating seamless collaboration between different teams, departments, and factory locations. Features like instant messaging, document sharing, and task management in a mobile app form enable real-time communication, fostering a culture of teamwork. Improved communication promotes swift issue resolution, better coordination, and enhanced operational agility.
Streamlining Operations
Mobile apps digitize and automate various processes, eliminating manual data entry and reducing the risk of human error. Customizable mobile forms digitize paper-based forms, checklists, and surveys, simplifying data collection. Certain mobile apps also allow for the automation of routine tasks, such as equipment maintenance scheduling and inventory management. These streamlined operations lead to increased productivity and operational efficiency. Another study by McKinsey found that digitized factories can achieve up to a 30% reduction in costs, indicating the potential cost-saving benefits of mobile app-driven digitization.
Leveraging Advanced Analytics
Factory digitization also enables manufacturers to leverage advanced analytics for data-driven decision-making. Robust analytics capabilities track key performance indicators, identify bottlenecks, and provide valuable insights. By analyzing data, manufacturers can optimize production processes, improve resource utilization, and drive continuous improvement initiatives. Deloitte's research emphasizes that embracing digital transformation can make manufacturers 26% more profitable than their non-digitized counterparts.
Embracing Innovation
Factory digitization paves the way for manufacturers to embrace innovation and emerging technologies. Mobile apps serve as a foundation for integrating technologies like artificial intelligence, machine learning, and augmented reality into factory operations. ReadyKey's flexible and scalable architecture in particular, allows seamless integration with these technologies, future-proofing factories and ensuring their readiness for Industry 4.0.
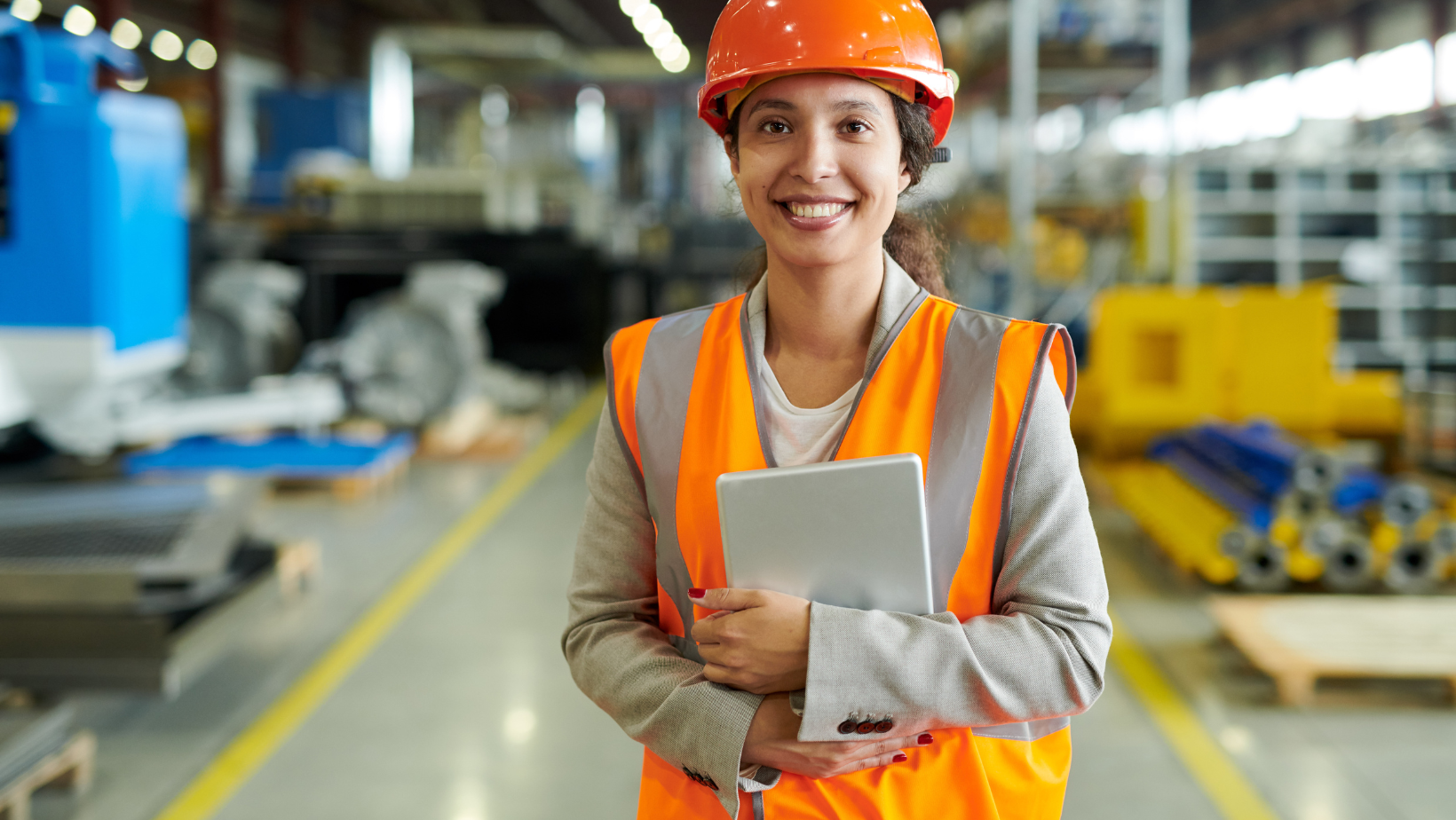
A Mobile-First Strategy
It would be remiss of us not to highlight some of the unique features that the ReadyKey platform offers that can support the digitization process and address the challenges faced by manufacturers. By leveraging these powerful tools, manufacturers can enhance digitization, improve information access, boost data quality and engagement, and reduce costs associated with paper-based systems. ReadyKey empowers factories to transition smoothly to digital workflows, making it a valuable tool for achieving efficient and profitable digitization in manufacturing. Here are some of the key ReadyKey-specific features:
QR Code Accessing
ReadyKey allows you to utilize QR codes to support your digital factory strategy. By placing QR codes on machines, doors, walls, and vehicles, you can provide instant access to relevant information when and where it's needed. This feature eliminates the need for manual documentation and enables real-time updates without the hassle and cost of printing new paper documents. With QR code access, employees can quickly retrieve safety information, instructions, or updates, enhancing operational efficiency and accuracy.
.gif)
Fully Customizable Mobile Forms
ReadyKey helps transform data collection by moving away from paper-based forms, checklists, and reports. With fully customizable mobile forms, manufacturers can increase the quality of data collection while improving employee engagement. The mobile forms simplify the logging process by providing accurate dates and times, ensuring compliance with regulations such as OSHA. In addition, features such as seamless photo and video upload allow users to submit accurate and pertinent safety reports, machine logs, and more. By digitizing data collection, ReadyKey streamlines reporting processes, reduces errors, and encourages active participation from employees.
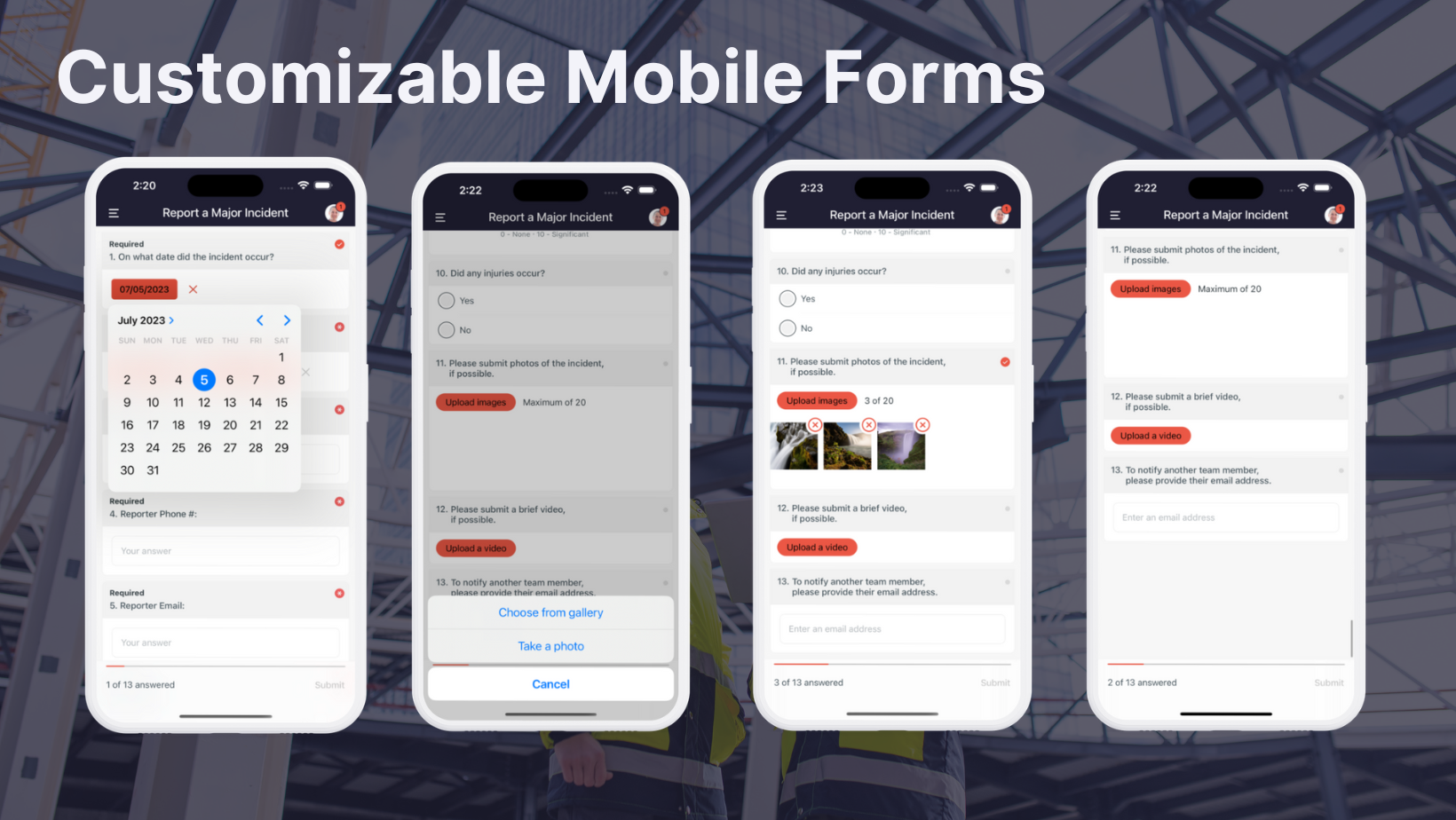
Management of Change Made Easy
Keeping paper documents up-to-date can be costly, with an average cost of $600-1000 per location, per year. ReadyKey's mobile app simplifies the management of change by allowing quick and easy updates that reach employees in real time. This feature eliminates the need for printing and distributing physical documents, significantly reducing costs. With ReadyKey’s award-winning CMS platform, manufacturers can efficiently and easily communicate changes, updates, and instructions to employees, ensuring everyone is on the same page without incurring unnecessary expenses.
Unlocking the Digital Revolution
In the fast-paced world of manufacturing, mobile apps are emerging as game-changers, modernizing factory digitization. They tackle the pain points of manual systems, communication bottlenecks, and inefficient data analysis head-on, unleashing a new era of efficiency and profitability. Imagine a world where QR codes provide instant access to critical information, where customizable mobile forms make data collection a breeze, and where change management becomes a seamless process. It's all within reach with mobile apps like those built on the ReadyKey platform. By embracing a mobile-first strategy and harnessing these tools, manufacturers can unlock the door to efficient and profitable digitization, propelling themselves ahead in the competitive race. It's time to embrace the power of mobile apps and take manufacturing to exhilarating new heights.