This is part two of a three-part series focused on OSHA’s Process Safety Management (PSM) standard. In this post we’ll focus on a handful of compliance and performance best practices that you may find useful as you focus on reducing risks related to process safety. If you missed the first post, An Introduction to OSHA’s Process Safety Management Standard, let’s briefly review a bit of PSM background to help set the stage:
- OSHA’s PSM standard has been in place since 1992 and, with few exceptions, applies to any non-retail facility with industrial processes that store, use, handle, manufacture, and/or move highly hazardous chemicals in quantities exceeding specified threshold quantities.
- The PSM standard lays out a multi-layered management system framework for reducing process safety-related risk and includes 14 interconnected elements designed to help facilities identify and control hazards associated with highly hazardous chemicals and assure the safety of workers and the environment.
- Effective execution of the PSM management system elements will reduce a facility’s risk of highly hazardous chemical incidents. But how do we achieve that level of performance?
Achieving top-notch performance takes work, not only on the individual tactics needed to install each of the 14 PSM management system elements in and across our facilities but more importantly on the strategies we identify and deploy to organize the work to shape effective, well-executed, and sustainable PSM elements.
We can break this down further by thinking about the work as three overarching, interlinked components – Process, People, and Platforms – and providing a few best practice examples of each.
PSM is designed to be a performance-based standard, so the examples we supply below should be taken as starting points for your own thinking around your own facility-specific PSM strategies and compliance needs.
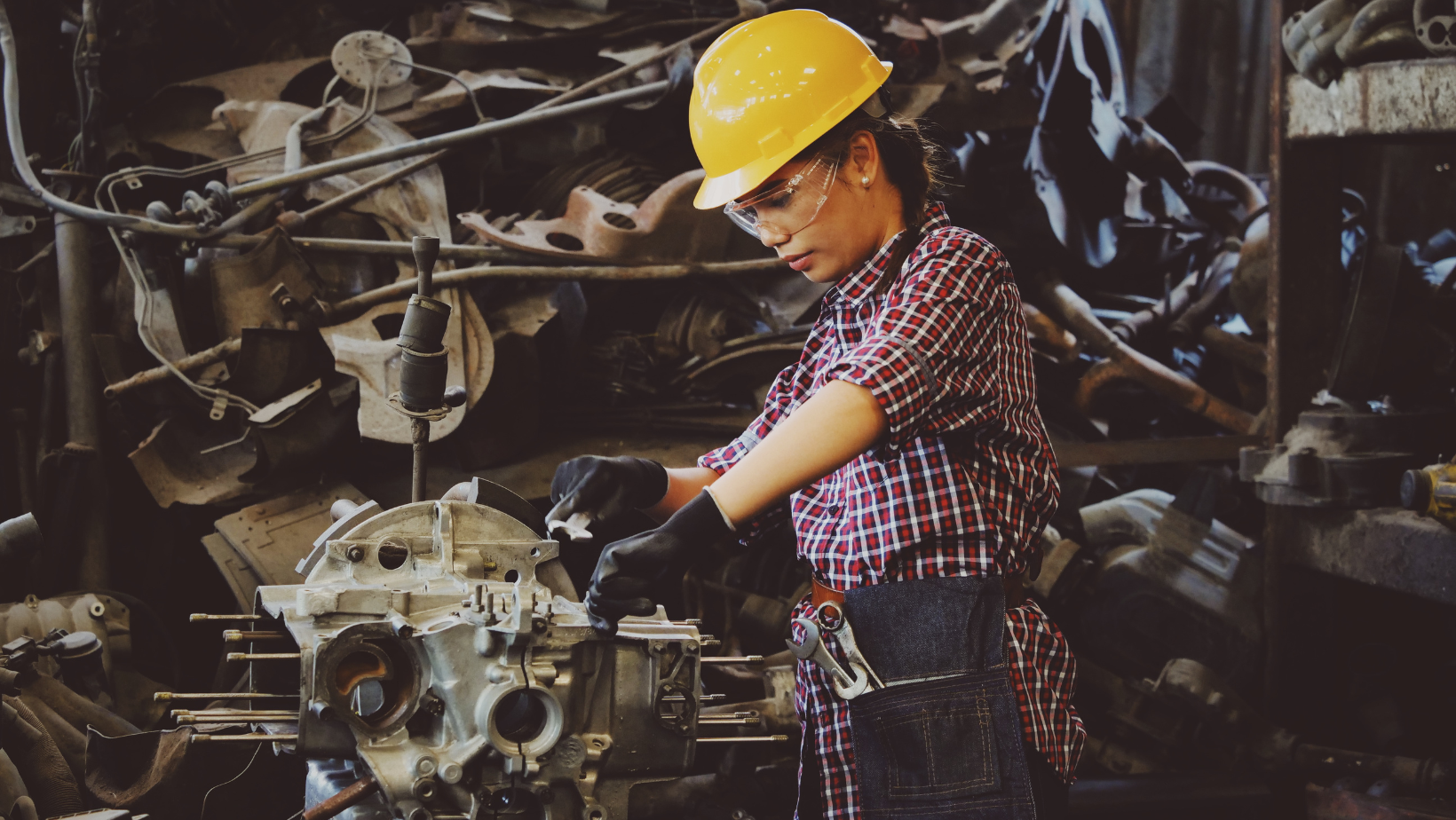
Process: Best Practices for Reducing PSM-Related Risks
An initial key to success is to align your PSM elements with your facility’s existing EHS and Operations programs and workflows to the greatest extent possible. We focus on this aspect primarily to avoid creating unnecessary and resource-draining barriers to facility adoption, but also because we don’t want to go out of our way to change existing processes and workflows that are already working (if it ain’t broke, don’t fix it). Remember, everyone has more than enough work on their hands already – we don’t need to go creating additional work for our facilities and/or ourselves.
A good example of this concept is utilizing your facility’s existing Emergency Planning and Response (EPR) program as the basis for your PSM-compliant EPR program. For example, let’s assume you have an existing Integrated Contingency Plan (ICP) that your facility uses to meet its RCRA and OSHA emergency response compliance requirements. Your ICP has been fully adopted by your facility and is working well to effectively reduce emergency response-related risk. It makes sense then to take your ICP, tweak it only to the extent needed to assure that it fully addresses your PSM highly hazardous chemical(s), and incorporate it to meet your PSM EPR compliance needs.
Similarly, your facility’s Hot Work (and other safe work practices such as Lockout Tagout, Work at Height, Confined Space Entry) should readily form the basis for your PSM Hot Work Permit compliance needs. We can take this thought a step further by utilizing your facility’s existing HazCom programs and practices (e.g., Safety Data Sheets) to support your PSM Process Safety Information compliance needs.
The key here is to avoid “bolt-on” programs to the maximum extent practicable. Note though, this requires the ability to clearly see where new PSM-specific programs may or will be warranted.
For example, suppose the chemicals at your facility do not exceed PSM-specified threshold quantities and pose a low risk of a catastrophic release, low enough that your facility has only implemented informal Employee Participation, Process Hazard Analysis, and Management of Change programs. Plans are afoot, however, to increase the existing chemical inventory or risk (think OSHA General Duty Clause requirements) or to introduce a PSM-regulated chemical. In this case, commensurate risk reduction will be required and your facility will need to implement formalized, PSM-compliant programs meeting the PSM regulatory requirements.
In summary, streamline the work required to implement PSM effectively at your facility while avoiding unnecessary change wherever possible. This will reduce the overall workload and remove barriers to the adoption of PSM-compliant risk-reduction programs.
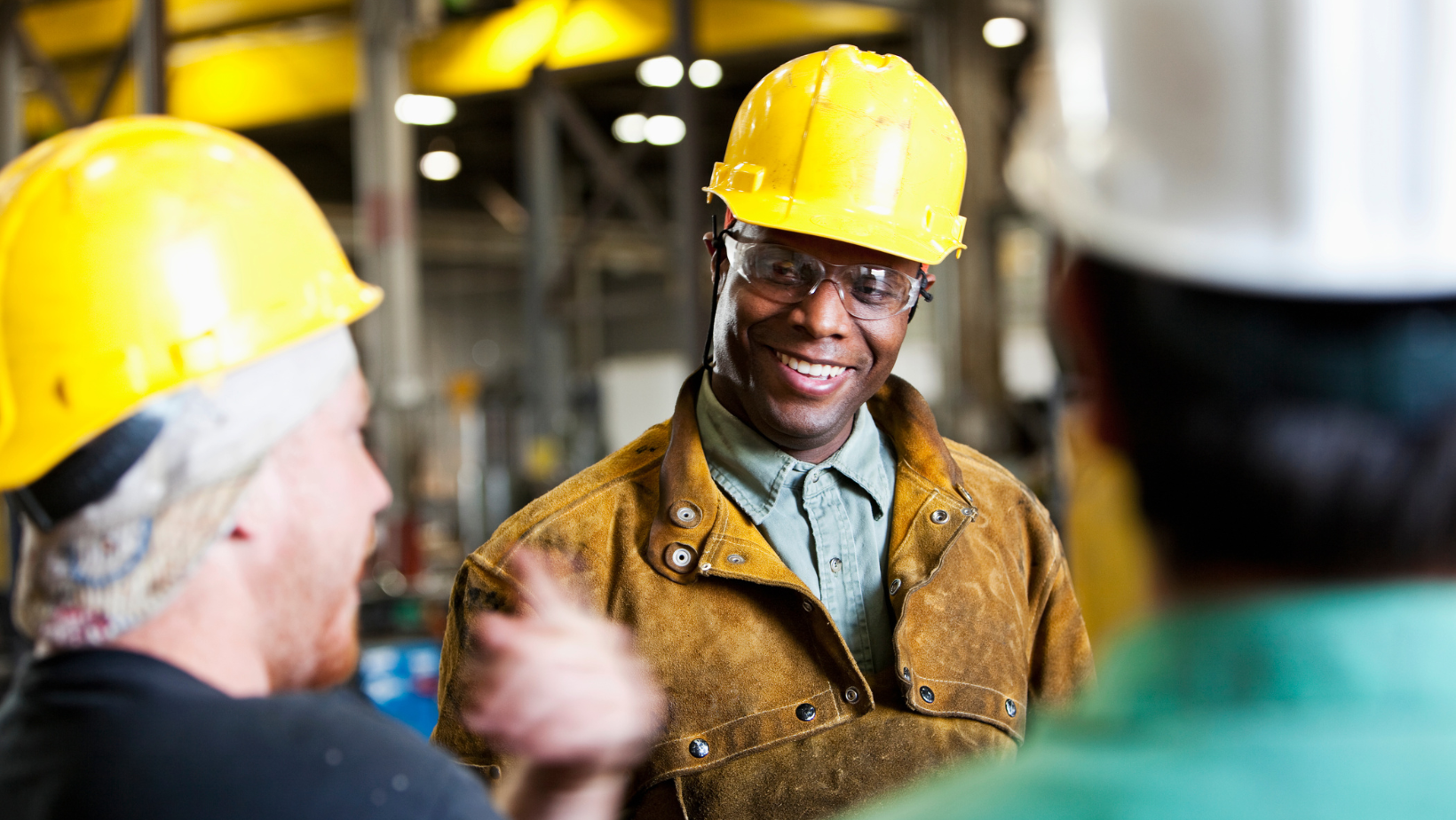
People: Best Practices for Reducing PSM-Related Risks
Of all the EHS truisms I picked up over my career, two stand out above all the rest:
- Leadership is the Foundation of Safety. Leadership standards and expectations are expressed during GEMBA walks and other leadership-employee interactions. Some examples include one-to-one conversations, employee listening sessions, and transparent incident investigations. Leaders that practice a Servant Leadership Style build a culture of trust - doing for others more than themselves, encouraging diversity of thought and input, and fostering leadership in all. By “walking the walk,” practicing Servant Leadership, and allocating the needed EHS-supporting resources, leaders can set the EHS performance foundation.
- People are the Key to Safety. All work gets done at the production/shop floor level, and high-level EHS performance is only achievable when employees are fully supported in, committed to, and work diligently toward the desired EHS outcome: For everyone to work and go home safely. Basically, without exception - every employee (including leaders) wants everyone to succeed in working and going home safely. No one intentionally takes a day off with respect to this pursuit.
So what does this mean in practice with respect to PSM in particular? For starters, it means that the greater your employees’ involvement in the development, implementation, and execution of your facility’s PSM program elements and the greater your employees’ knowledge of your facility’s industrial systems, procedures, and safeguards, the greater your odds of successfully preventing catastrophic releases.
Focus on assuring your employees’ understanding of the overarching, interconnected framework of PSM elements and the specific roles they fill with respect to each element. It is imperative that Operations and Maintenance employees participate in Process Hazard Analyses, Operations and Maintenance Procedure development and review, and Incident Investigations to assure unfettered inclusion of pertinent production and shop floor knowledge to assure ongoing continuous risk reduction improvement.
Training (initial, refresher, emergency response, contractor) needs to clearly and effectively communicate the hazards of the chemicals people work with, the procedures and processes that are used to control and manage the risks relating to these hazards, and the procedures that must be followed to prevent and/or respond to catastrophic releases.
Access to (and appropriate understanding of) the facility’s Process Safety Information is vital as is appropriate training on the pertinent equipment technologies. Consideration should be given to industry certifications as a means to assure a baseline employee performance capability. For example, facilities utilizing industrial refrigerants such as ammonia might consider appropriate Refrigerating Engineers and Technicians Association (RETA) training and certification such as the entry level Certified Assistant Refrigeration Operator (CARO) or more advanced level Certified Industrial Refrigeration Operator (CIRO) certifications.
In summary, Leadership and employees working in partnership will enable the achievement of a topflight PSM program. Safety starts with Leadership; Safety’s key is people.
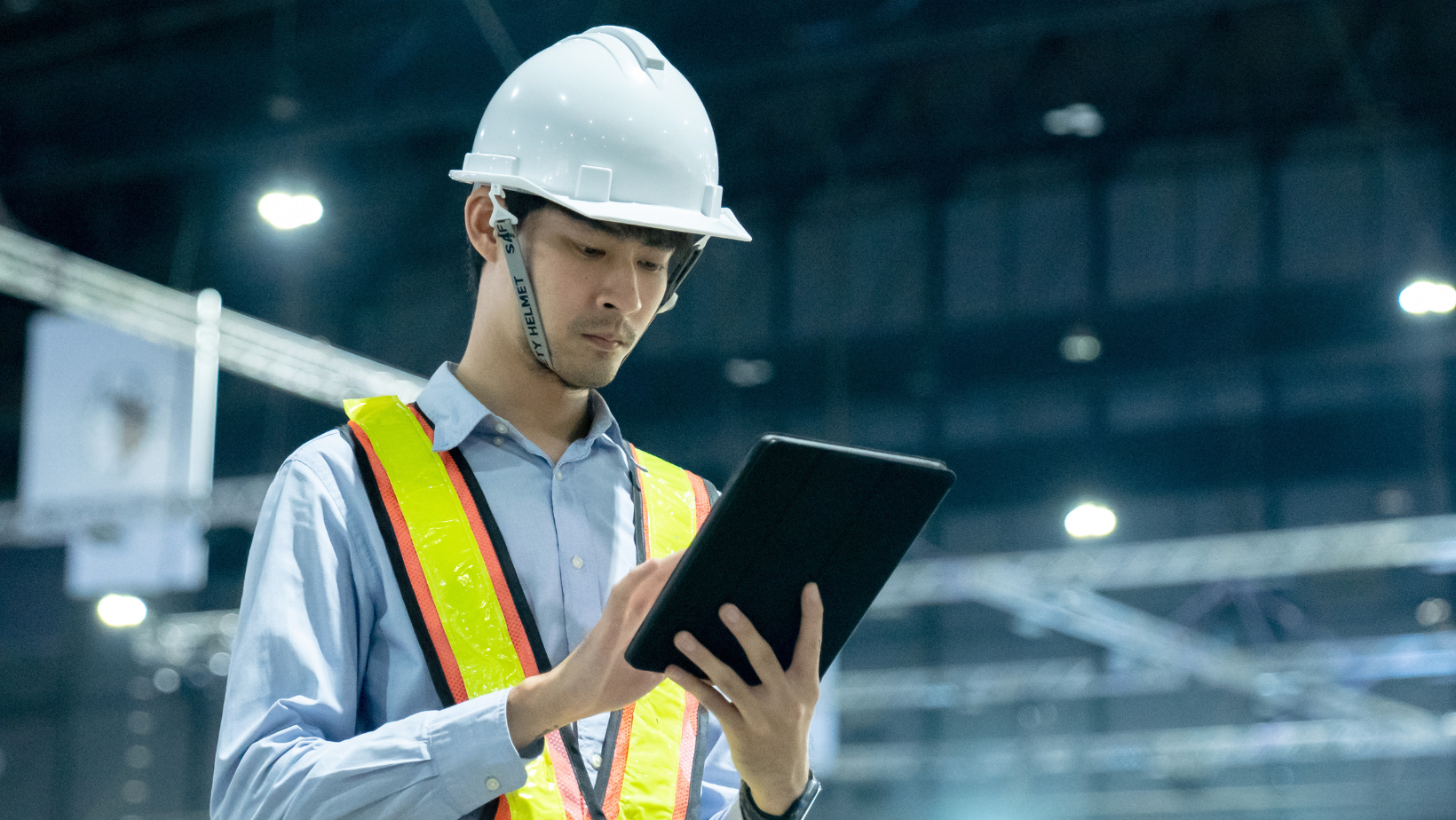
Platforms: Best Practices for Reducing PSM-Related Risks
Aligning your PSM processes with knowledgeable, engaged employees enables higher-level EHS performance. But to reach topflight performance requires a third ingredient: The right platform. Platforms can take many forms across a broad spectrum, from software productivity suites to integrated risk management software packages to handheld mobile apps. Each has its place. Each has its advantages and disadvantages. The key is to match the right platform to the right roles so that the right process information is in the right people’s hands at the right time.
While productivity suites and risk management packages have been widely available and in use for many years, mobile apps are a more recent arrival having arisen largely in conjunction with society’s exponentially increasing adoption and use of mobile phones and other mobile devices.
When selecting one’s choice of technology it is always a good idea to consider your overarching vision and expectations relating to your objectives and required capabilities and to clearly demarcate your must-haves from your high-wants. Your goal is not to select the most whiz-bang, high-tech platform available but rather to get all of your must-haves and as many of your high-wants as possible in the most reliable, sustainable, and cost-effective manner.
One of your key considerations in the choice of platform should focus on the “familiarity factor.” You may determine that your employees are already widely familiar and comfortable with a particular platform. In this case, as we saw earlier, we focus here primarily to avoid creating unnecessary and resource-draining barriers to adoption. Leveraging familiarity is a great strategy for doing just this.
One of your earliest decision points will be whether to focus on a more traditional cloud or PC-based productivity suite or risk management platforms or to pursue a mobile-first approach. Keep in mind that you may end up identifying a mixture of platforms as your ideal solution. In all cases, collaboration with a team of front-line employees, IT, EHS, and Operations experts will be critical to assure that all stakeholder needs and inputs are properly addressed so that you hit your marks to the best of your ability.
Let’s consider a PSM Emergency Planning and Response example at a facility that has elected to limit its response to defensive actions while leaving outside First Responder teams representing fire, emergency medical services, law enforcement, and other public safety entities to take the needed offensive actions. In this case, your facility’s emergency response leaders and team members will have received training in and be called upon to safely and effectively mitigate the hazards presented until such time as outside First Responders arrive onsite. Let's take a look at what your team must have, what they likely want to have, and some things to consider.
Things Your Team Must Have
Your people will need real-time, on-the-go access to your facility’s current emergency response procedures covering topics such as:
- How releases are identified and by whom
- How your facility’s Incident Command is initiated, and by whom
- How initial risk assessments are made and by whom
- What initial defensive actions are taken and by whom
- How initial and follow-up notifications (both internal and external) are made (email, text, and/or phone) and by whom
- How Incident Command will be transferred to outside First Responders and what Unified Command steps will be required by facility personnel
- How incident termination is determined and by whom
Things Your Team Wants
In addition, your people will likely desire
- Inclusion of current emergency contact information (both internal and external)
- Ready access to key facility plot plans, drawings, utility diagrams, regulatory spill/stormwater plans, etc
- Ready access to all of the above information via their mobile devices (familiarity factor)
Things to Consider: Productivity Suites, Integrated Risk Management Packages, and Mobile Apps
The enormously useful and ubiquitous productivity suites have long been a tool of choice for many of us. In my career as an EHS engineer, Microsoft Excel proved essential as a robust data organization, management, and synthesis tool, allowing me to synthesize multiple, oftentimes disparate data and create or present models (statistical and otherwise) to inform sound decision-making.
Specific to process safety and PSM, Excel formed the platform basis for enterprise-wide, multi-facility risk assessments incorporating multiple inputs relating to equipment age, complexity, design, conformance to industry standards, potential for offsite consequences, and mechanical condition to create an overarching risk ranking used to prioritize ongoing and future risk reduction efforts.
Excel and other similar tools are still important, but as technology has evolved, mobile apps, like EHS apps built on the ReadyKey platform, have emerged as an advantage in today’s mobile device-focused world. The advantage is that employees have access to the critical information needed to address the issue immediately at hand, anyplace, anytime.
Summary
So what are we really trying to say here? While PSM compliance is a unique subject area, PSM performance assurance is not necessarily a unique structure. Understanding that people are one of the keys to a highly performing PSM program, and understanding the importance of aligning processes and platforms to those stakeholders, is critical to your overall success. Organizations that have the greatest written PSM programs on the planet will fail to control their risk if they don’t engage the right stakeholders, and don’t align their platform investments accordingly.
Read the rest of the series
Read part 1
Read part 3